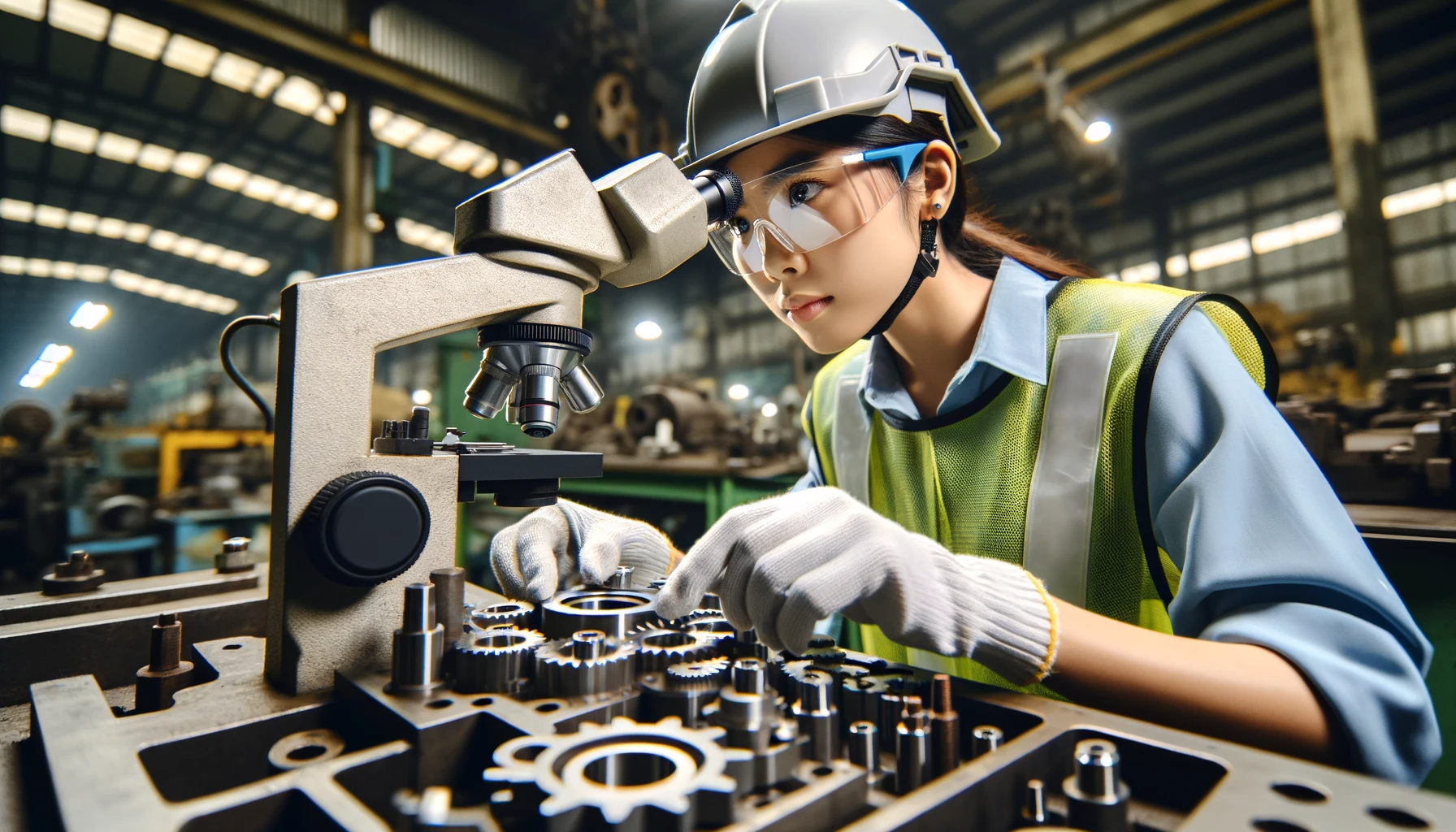
In traditional manufacturing settings, visual inspection (inspection tasks to confirm the surface of products or components) has long been carried out by experienced and skilled personnel.
In recent years, Japan's manufacturing industry has been facing challenges such as an aging workforce and a declining interest among younger generations in manufacturing careers. As a result, continuing inspection tasks in the traditional manner has become increasingly difficult.
One of the alternatives to visual appearance inspection, which tends to be a highly human-dependent task, is the use of image processing technology. Before exploring the application of image technology, let's take a look at the current state and challenges of visual appearance inspection.
1. Purpose of Visual Appearance Inspection
Defects identified through visual inspection can be broadly categorized into "functional defects" and "aesthetic defects." The primary objective is to accurately distinguish between pass and fail items to prevent defective products from progressing to subsequent processes or reaching customers.
(1) Functional Defects
In this case, defects that could affect the performance or function of the product are identified through visual inspection.
One might question, "Are functional defects being identified through visual inspection?"
However, for instance, in cases where products exhibit cracks or chips, these defects may be considered as factors affecting the functional performance of the product, particularly in situations where mechanical characteristics are required.
(2) Aesthetic Defects
This is a case where defects that may not directly impact the performance or functionality of a product are identified through visual inspection but could still be perceived as defects by end users based on appearance alone. Especially for products intended for general consumers and applied to visible areas, there tends to be a strict identification of aesthetic defects.
In any case, differences in size and color are evaluated and judged against a reference sample to determine acceptability. The determination through visual inspection has the advantage of not requiring special equipment, thus incurs no initial cost.
However, it is also true that visual inspection is a process heavily dependent on humans and carries issues that are "unique to humans."
Challenges of Visual Appearance Inspection
2. Targets of Visual Appearance Inspection
(1)Presence or Absence of Target Objects
- Confirmation of missing assembly parts in assembled products (e.g., missing screws)
- Confirmation of processing omissions (e.g., forgotten drilling operations)
- Confirmation of missing items in packaged products containing multiple varieties (e.g., ensuring all items are included in bento boxes)
(2) The Spatial Relationship of Target Objects
- Confirmation of the spatial relationship of assembled products (e.g., parts not properly fitted into position, resulting in gaps)
- Confirmation of alignment with intended locations (e.g., ensuring correct parts are assembled in their designated positions)
(3) Surface Condition and Shape
- Verification of product surface condition (e.g., color discrepancies, foreign material adhesion, cracks)
- Verification of product shape and dimensions (e.g., product chipping, dimensional defects)
3. Summary
In this way, visual inspection is an indispensable process to prevent defective products from reaching subsequent processes or customers. However, defects identifiable through visual inspection vary widely, and the current situation involves flexible adaptation based on inspection criteria and rules, leveraging human flexibility depending on the target product and the desired identification criteria.
Related Links
Challenges of Visual Appearance Inspection
Alternative Methods to Visual Determination