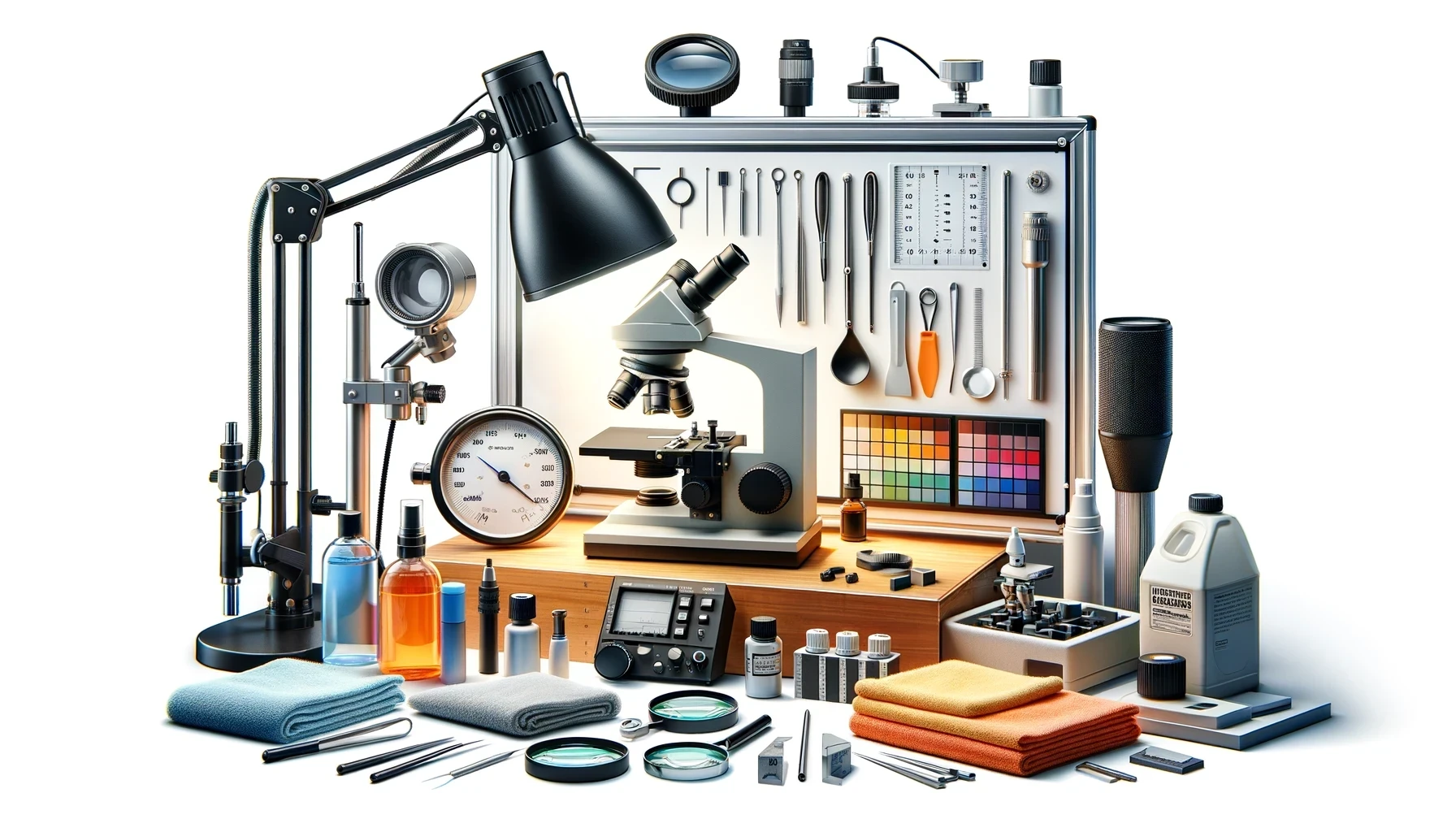
As explained in "Purpose of Appearance Inspection and Determination Details", visual determination is a critical element of quality assurance. The quality of a product is directly linked to the reliability of a company, and to ensure that quality, an accurate and consistent inspection process is essential. However, visual appearance inspection also presents various challenges.
1. Accuracy and Stability of Precision
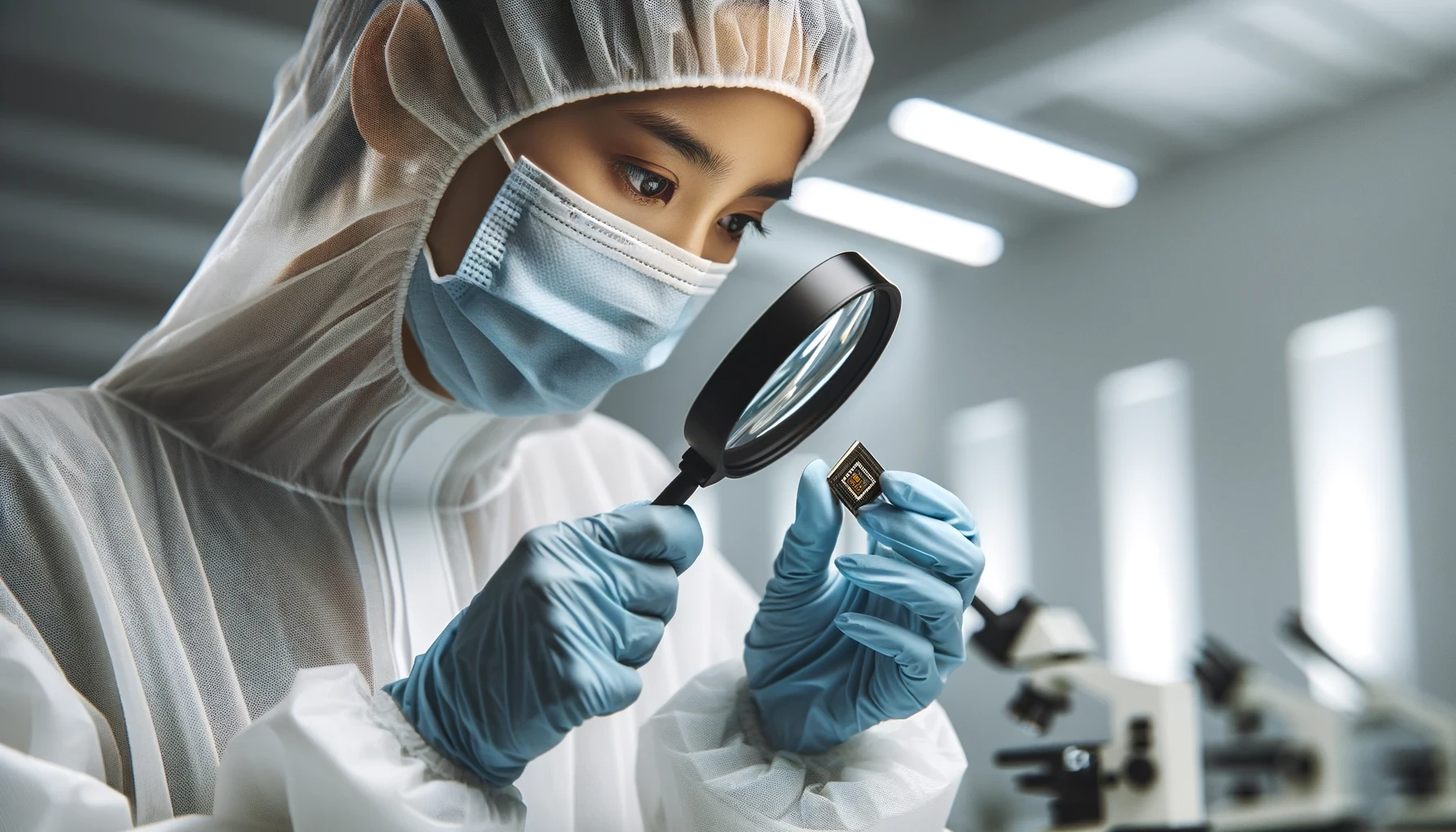
In human visual inspection, individuals rely on their experience to inspect various aspects such as how light is directed onto the product surface, where defects are likely to occur, and the acceptable range for a defect-free product, including identifying minor scratches or subtle color differences. Factors such as fatigue, health conditions, and decreased attention can influence inspection results. Additionally, the surrounding environment, the inspector's level of expertise, and personal characteristics can also significantly impact the inspection process.
2. Education
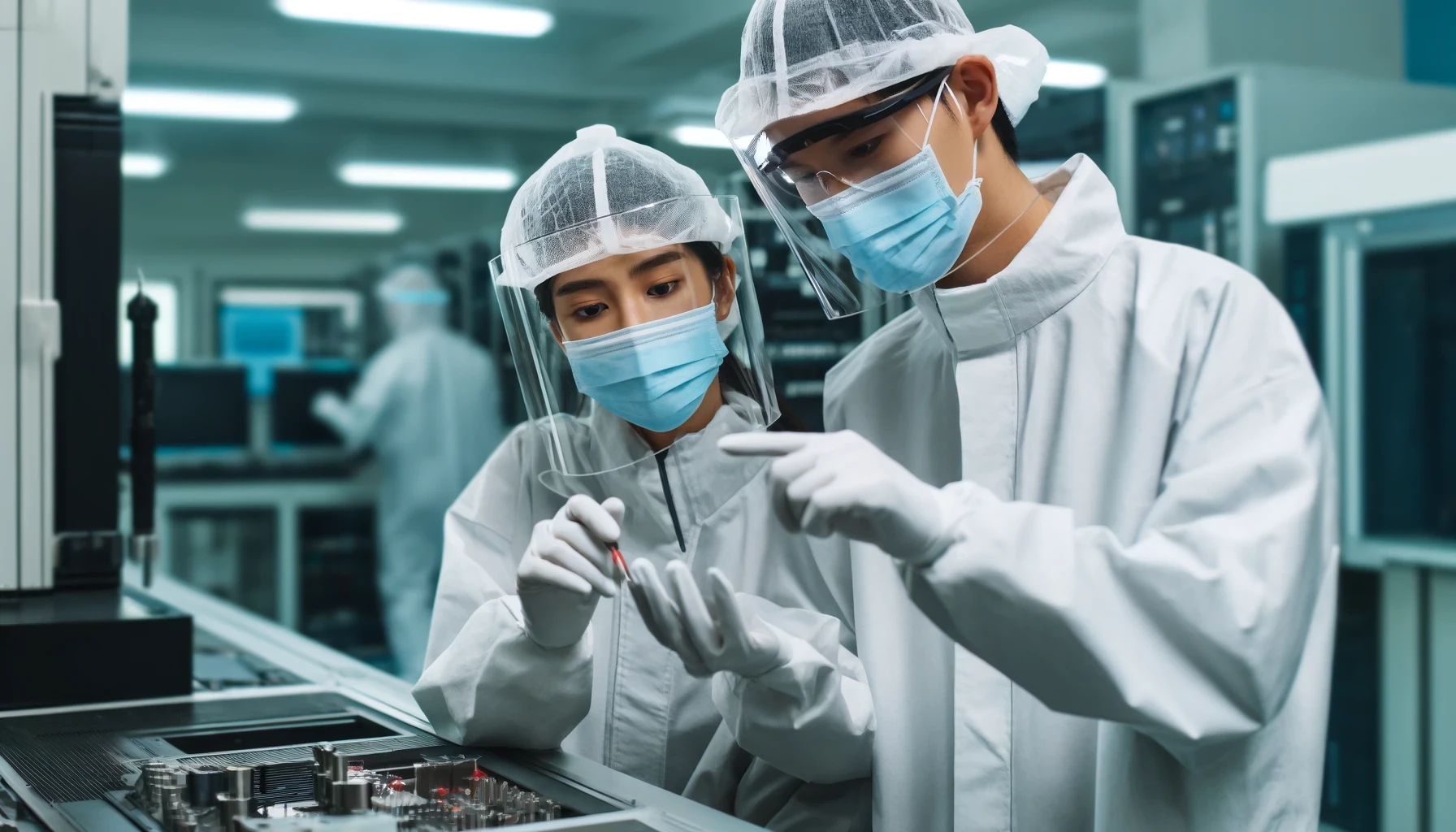
Visual inspection demands high skills and experience, thus, extensive education is required for the training of new inspectors. Furthermore, education involves systematic learning through documents such as inspection instructions, and accumulating experiential knowledge of the characteristics of pass and fail products by becoming familiar with actual products. Recognizing the hidden costs and time involved from inspector recruitment to education is essential for conducting accurate inspections.
3. Traceability
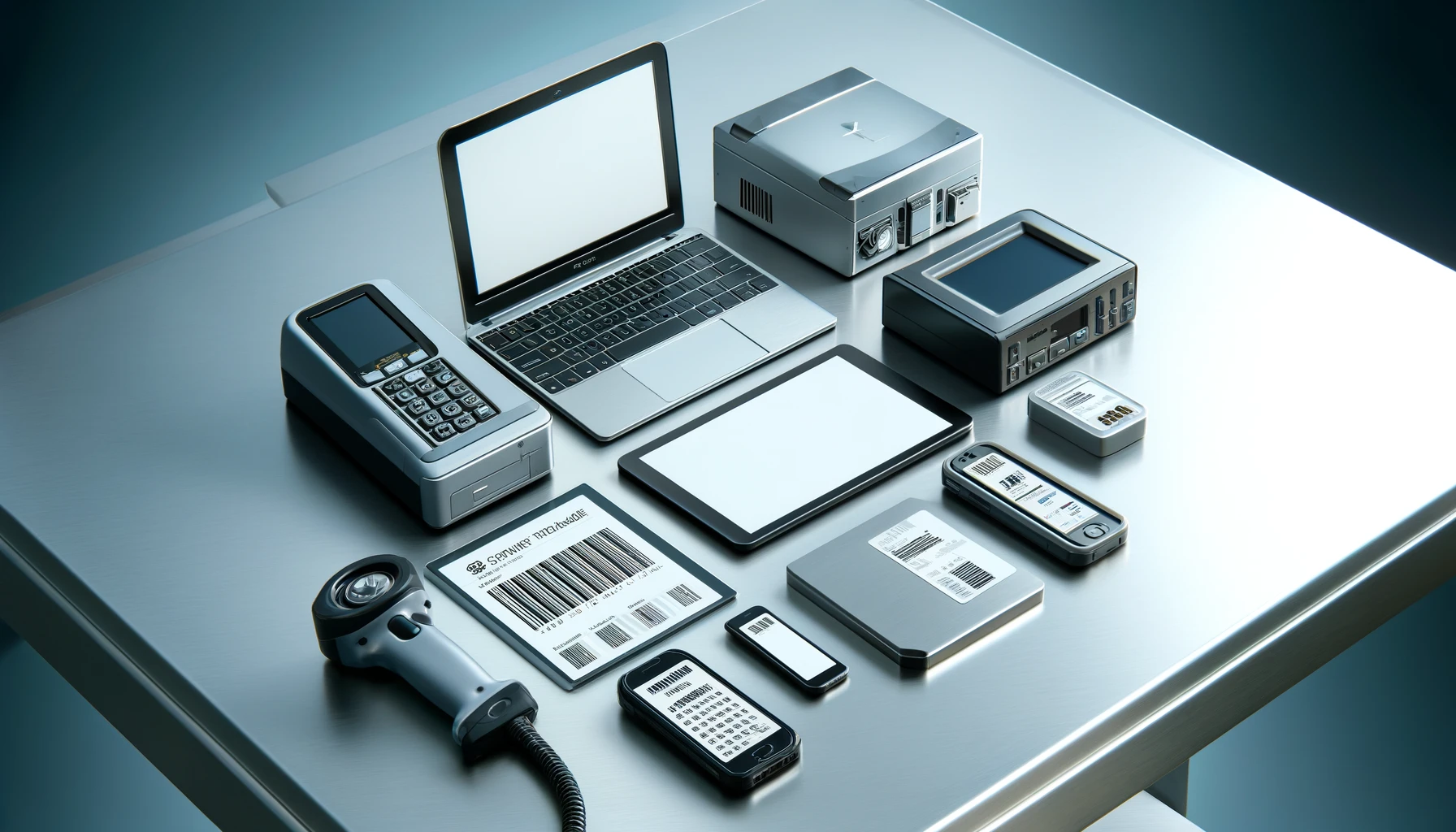
In visual inspection, people simply use their eyes to identify pass/fail products on the spot. As a result, only the number and types of defects detected are recorded, and most often, the data is not saved in formats such as image files.
Therefore, once defective products have leaked into subsequent processes or reached customers, it becomes practically impossible to trace whether "the inspection was actually conducted." Even if pursued by subsequent processes or customers for "overlooking" defects, it is difficult to verify the reality.
Moreover, various data, such as the product condition before and after defect occurrence, the timing of defect occurrence, and production conditions at the time of occurrence, could potentially improve yield if the cause of the defects is pursued and resolved. However, since inspectors focus solely on "reliably identifying defective products," cases are frequently observed where efforts to prevent or suppress defect recurrence are not undertaken.
4. Summary
As explained so far, visual appearance inspection fundamentally relies on the "presence of diligent and tireless inspectors." One solution to this challenge is the utilization of visual inspection systems that incorporate image processing technology. Determination systems based on image processing technology not only help to break away from the human-dependent nature of visual inspection, but also hold the potential for improving quality and productivity through the utilization of the collected data.