
The necessary technologies include "Technologies Related to Image Acquisition (technologies that substitute for the 'eyes' in visual determination)," "Technologies Involved to in Pass/Fail Classification (technologies associated with the 'brain' in visual determination)," and "Technologies for Data Utilization".
The first essential technology is "Technologies Related to Image Acquisition (technologies that substitute for the 'eyes' in visual determination)," which involves acquiring images for inspection purposes. Image acquisition requires a "camera" for capturing images, a "lens" to determine the imaging range, and "illumination" to enhance the visibility of the inspection areas.
1. About Cameras
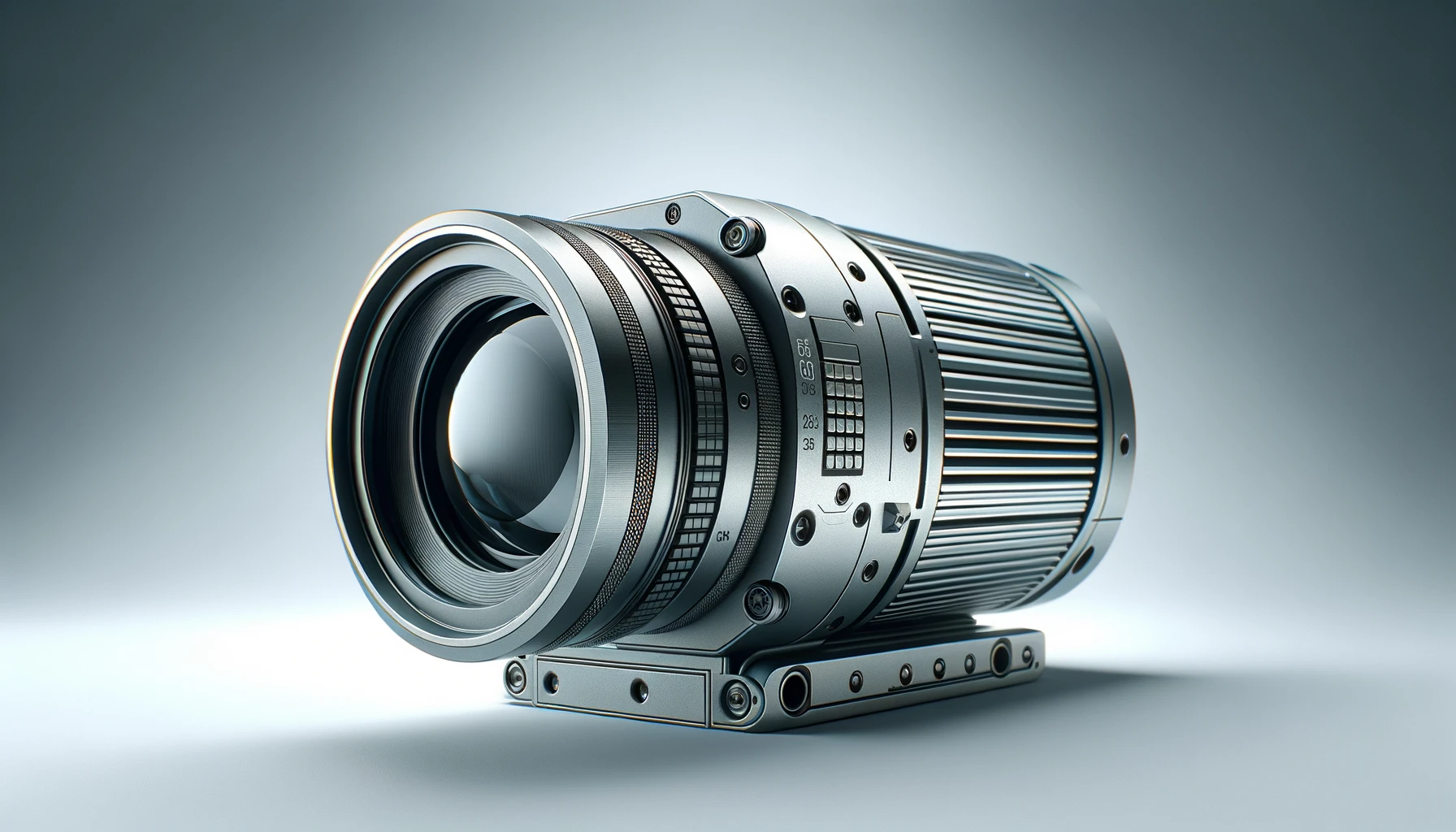
Cameras come in two main types: consumer cameras, which we usually encounter in daily life, and industrial cameras, primarily used on production lines and similar settings.
Consumer cameras are characterized by their multifunctionality, including features like autofocus and color adjustment.
On the other hand, industrial cameras are known for their durability and ability to operate continuously in various environments, ensuring stable imaging.
In this discussion, we will explain the selection criteria for industrial cameras.
(1) Types
Mainly, they are classified into two types: network (IP) cameras and machine vision cameras.
Network cameras are widely used for surveillance purposes, while machine vision cameras are used for image processing in tasks such as inspection on manufacturing lines, medical applications, and research fields.
Network cameras often come integrated with lenses, making them inexpensive and easy to connect compared to machine vision cameras. However, they are not suitable for detailed adjustments like machine vision cameras.
Machine vision cameras allow for the construction of optimal environments by considering factors such as resolution, type, and lens, but they require a certain level of expertise.
(2) Area Cameras and Line Scan Cameras
Machine vision cameras are classified into area cameras and line scan cameras based on the arrangement of the sensors.
Area cameras arrange the sensors in a grid pattern (vertical × horizontal) to capture a two-dimensional image in a single shot. Line scan cameras arrange the sensors in a single row to capture a one-dimensional image. By moving the product or camera in one direction while capturing images, a two-dimensional image is obtained by lining up the one-dimensional images.
Area cameras can capture a wide range at once, making installation easy; however, it is necessary to light the area to be determined evenly.
Line scan cameras only require uniform lighting along the one-dimensional line captured by the sensor, making the selection of lighting easier. However, this makes the transport control of the product or camera more complex.
As each of these camera types has its own advantages and disadvantages, it's crucial to understand their characteristics and choose the appropriate one based on the type of image you want to capture.
(3) Resolution (Pixel Count)
Resolution (Pixel Count) determines the level of detail captured by the camera.
Based on the overall size of the target product and the size of the features to be detected (e.g., scratches, foreign objects), the required resolution is selected. As the imaging area within a single image becomes larger, the imaging area per pixel also becomes larger, making it difficult to see fine details.
Conversely, increasing the resolution (increasing pixel count) can lead to longer image acquisition and processing times, as well as increased data storage requirements.
Therefore, it is crucial to determine the optimal resolution based on the specific application requirements.
(4) Sensor Size
The sensor is the component that converts light captured through the lens into electrical signals.
The size of this sensor affects the amount of color information in the captured image and the overall size of the image itself.
A larger sensor size results in increased color information within the image and larger overall image size.
(5) Interface
Processing the captured image data requires a computer equipped with image analysis software.
There are various methods of connection between the camera and the computer, such as USB, GigE, Camera Link, and CoaXPress, and the choice of connection method depends on the type of camera and image analysis software.
Each method has different characteristics in terms of transfer speed, connection distance, and cost.
The commonly used USB connection is advantageous because it is easy to connect to many computers due to the presence of connection ports, but there is a possibility of noise generation when capturing images to a computer due to electromagnetic interference occurring in the manufacturing environment.
Additionally, GigE connection is resistant to noise from electromagnetic interference and is suitable for long-distance connections, but separate preparation for powering the camera is required.
2. About Lends
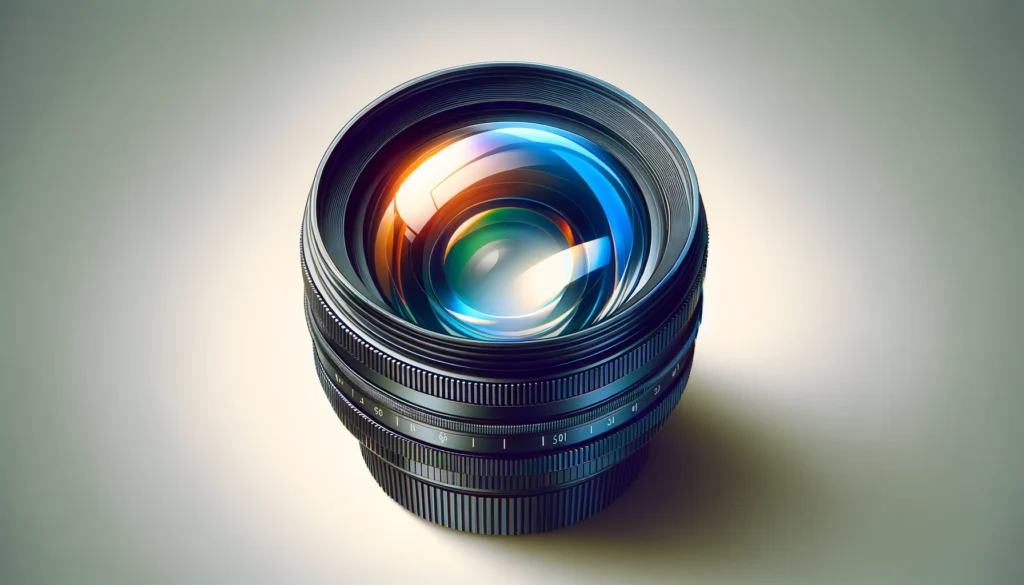
Choosing the right combination of camera and lens, tailored to the specific inspection subject and operating environment, is crucial for capturing the best possible image.
Understanding how the relationship between the lens's focal length, the desired imaging area, and the working distance between the lens and the product changes is necessary to achieve this.
Additionally, the relationship between the camera's sensor size and the lens is also crucial.
Consumer-grade cameras often use lenses compatible with autofocus functionality, but when performing image processing, manual adjustment of the focus is typically preferred due to potential issues with autofocus, such as focusing on unintended areas or requiring time to adjust the focus.
(1) Focal Length
The distance from the lens center to the imaging sensor is referred to as the focal length. The shorter the focal length, the wider the imaging range, while the longer the focal length, the narrower it becomes.
In general, lenses with short focal lengths have a greater distance difference between the center of the image and the edges, making it difficult to focus both the center and the edges.
Therefore, lenses with a focal length of 10mm or more are typically chosen.
(2) Distortion
The phenomenon where the image becomes distorted around the edges of the lens is known as distortion. The amount and location of distortion vary depending on the lens specifications and focal length.
Therefore, when selecting a lens, it is necessary to understand the extent of distortion that will occur and whether the distortion affects the areas critical to determination.
(3) The Impact of Camera Sensor Size
As the sensor size increases, a phenomenon called vignetting occurs where the lens housing is visible in the outer periphery of the imaging area, appearing black in the image.
Many lenses indicate the compatible camera sensor size, so it is crucial to confirm that the sensor size of the intended camera is supported when selecting a lens.
(4) Working Distance
The distance from the lens tip to the subject is what it means. The larger the working distance, the wider the imaging range, and the smaller the working distance, the narrower the imaging range.
Therefore, in lens selection, it is necessary to determine the optimal focal length within these constraint conditions after confirming the camera's sensor size, the required imaging range, and how much working distance can be achieved in the installation environment.
3. About Lighting
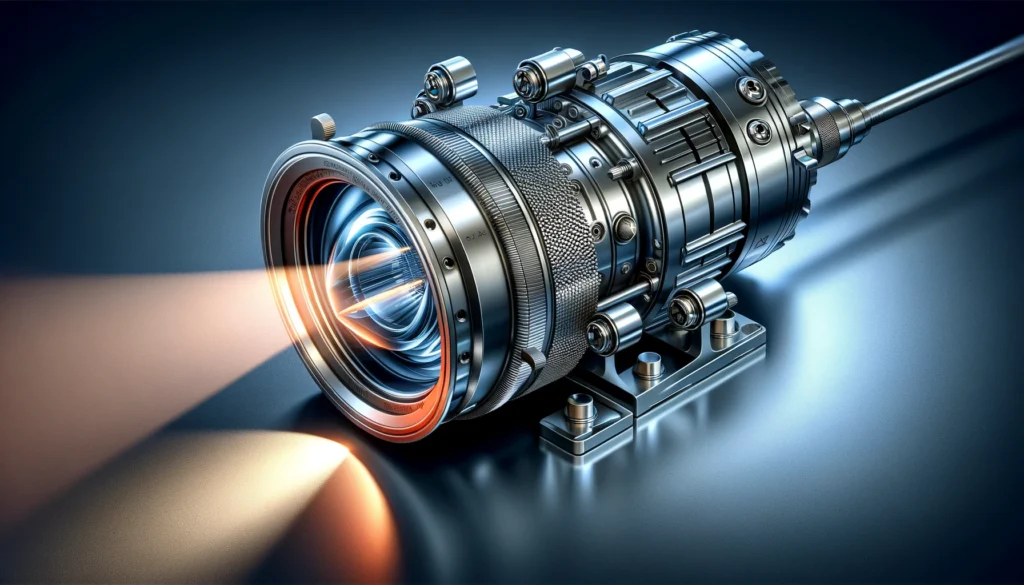
Lighting plays a crucial role in accurately extracting the features of an object. When capturing images of an object, lighting determines how effectively the image can be acquired.
For instance, by changing the type of lighting, adjustments can be made to the angle, color, and uniformity of the light.
No matter how excellent the camera and lens are, if the lighting selection is incorrect, it may not be possible to capture the target subject. Thus, lighting holds a crucial position in image processing.
(1) Direct Reflection Light, Diffuse Reflection Light, and Transmitted Light
By altering the type of lighting and the position of the lighting relative to the product under inspection, the type of light that the camera captures is selected. Direct reflected light uses lighting with a strong linear light component and captures light that is totally reflected from the surface of the product.Diffuse reflection light captures light that has been diffusely reflected by the product surface. Transmitted light captures light that has passed through the product.
Each has the following characteristics.
- Direct reflection light: This makes it easier to detect minor differences in the surface texture.
- Diffuse reflection light: The state that most closely resembles what is seen by the human eye is when diffused reflected light is captured. This makes it easier to capture color information and the texture of the product surface.
- Transmitted light: In the case of opaque products, using transmitted light increases the contrast at the edges of the product. This makes it easier to clearly capture the shape. Additionally, it is ideal for identifying inclusions within transparent products.
(2) Lighting Shape Adapted to Product Shape and Size
There are various types of lighting, including bar, ring, dome, and panel types. However, it is necessary to select the size and shape of the lighting that allows uniform lighting across the entire area to be inspected.
(3) Types of Light Wavelengths (Colors)
Short-wavelength (blue) light scatters easily on the surface of the product, allowing for bright imaging of fine scratches, while long-wavelength (red) light scatters less on the surface of the product, making it less susceptible to fine surface effects.
Additionally, for instance, when identifying black foreign objects on a red product, changing the wavelength of light to red can make the red parts appear white, making the black foreign objects more visible.
(4) Product and Lighting Arrangement
The positioning of the lighting relative to the product also significantly impacts the captured image.
For instance, when the light is directed at the product from a shallow angle (i.e., perpendicular to the camera's imaging direction), and the camera captures the reflected light, any shadows generated on the product surface can make it easier for the camera to capture information about surface irregularities.
Conversely, when the lighting is directed at the product from a steep angle (i.e., closer to the camera's imaging direction), it becomes difficult for the camera to capture surface irregularities, but it can more easily capture significant changes.
Thus, to "clearly identify the target subject" through the selection of lighting, adjustments considering various perspectives are necessary. This is a crucial and often challenging point in determination using image processing.
4. Summary
In this section, we provided detailed explanations about the key elements in the technology related to image acquisition: "Camera," "Lens," and "Lighting."
When conducting "defect detection utilizing image processing technology," there is a tendency to focus solely on image processing. However, no matter how advanced the image processing may be, correct identification cannot be achieved if defects are not captured in the image.
Therefore, it is crucial to select an appropriate combination of camera, lens, and lighting to ensure that the differences between defective and normal parts are clearly captured in the image, depending on the product to be inspected and the nature of the defects.