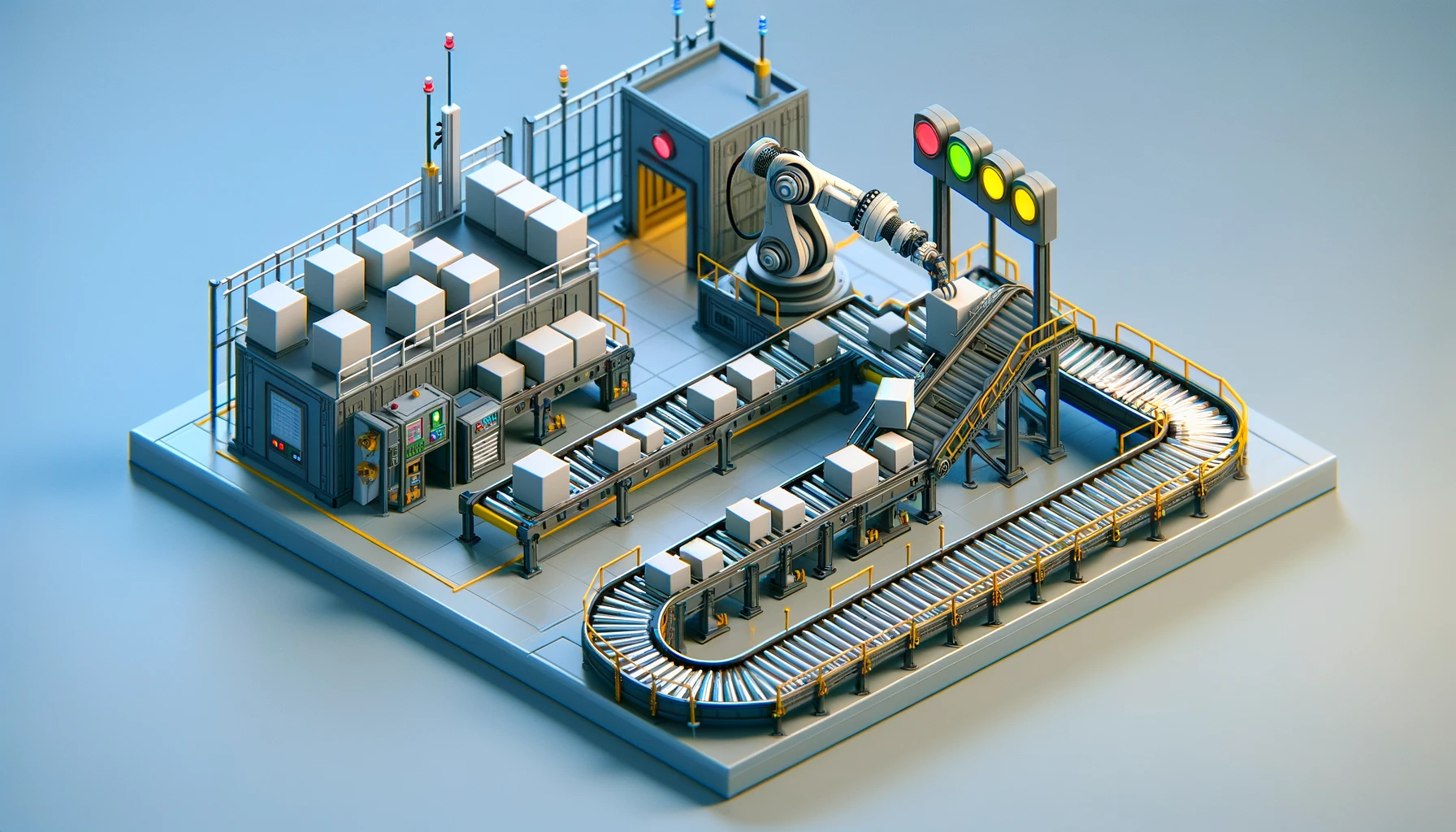
When implementing classification through image processing, it becomes crucial to consider alternative methods for tasks such as product retrieval, placement, focusing on determined surfaces, concentrating on details, and sorting according to classification results, tasks typically performed by humans during visual inspection.
Handling techniques for products play a pivotal role in fulfilling these functions.
Product handling encompasses essential tasks for the utilization of image processing systems, including retrieving products from production lines or trays, conveying them to the camera for imaging, optimal positioning of the camera and products, and the ejection or sorting of defective products upon detection.
In this context, we will explain these techniques, divided into "Position Control of Products and Cameras for Imaging" and "Conveyance and Sorting of Products."
1. Position Control of Products and Cameras for Imaging
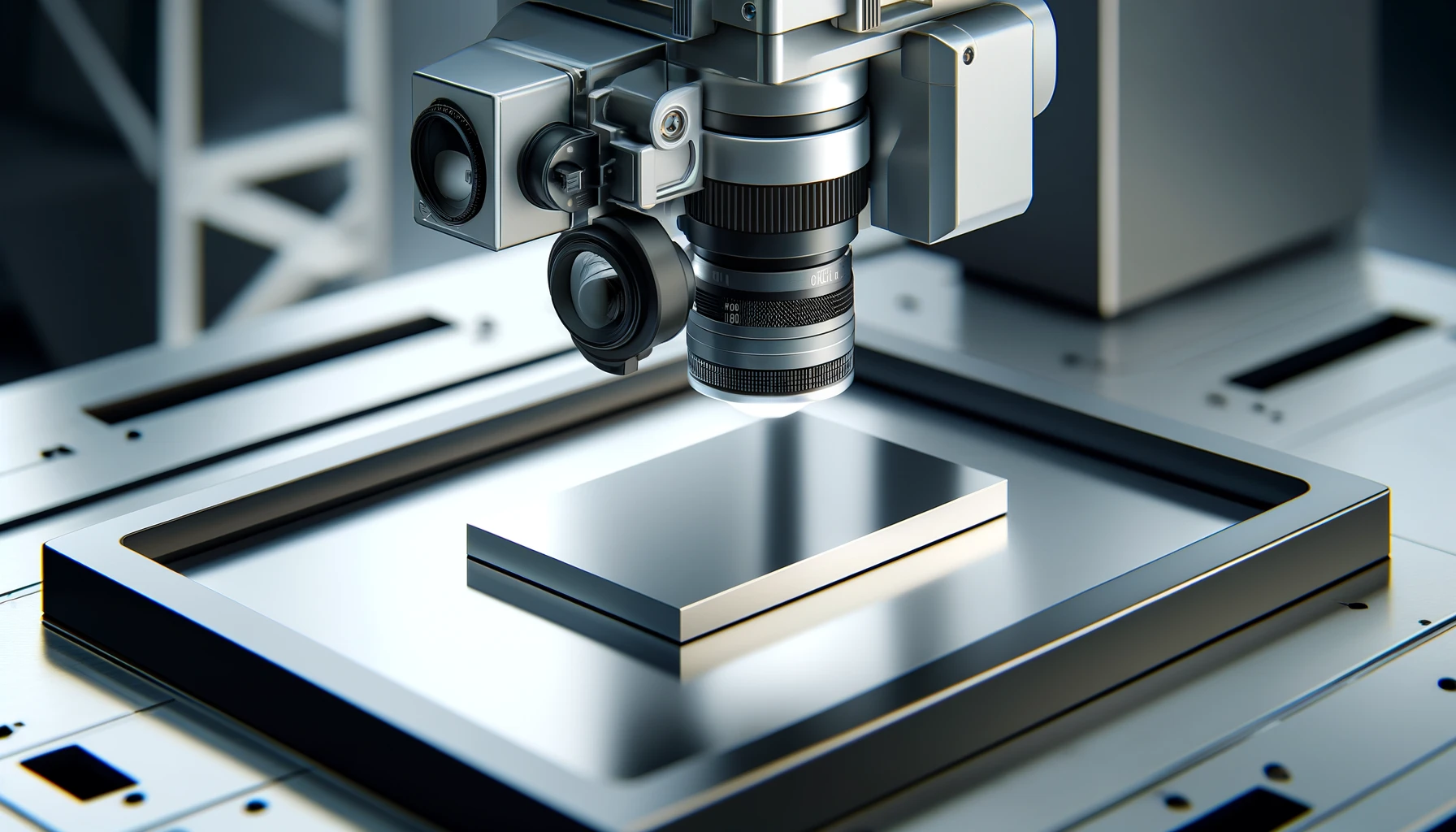
Conducting accurate inspections with image processing requires performing operations similar to those in visual inspections, where humans check the product from various directions to find defects.
Broadly, this involves two key elements: "Optimizing the Lighting" and "Eliminating Blind Spots in the Inspection Area."
(1) Optimizing the Lighting
One element of position control involves determining the angle at which to position the camera and lighting relative to the product surface.
As mentioned in "3. About Lighting in Technologies Related to Image Acquisition," the optimal spatial relationship among the camera, product, and lighting varies depending on what needs to be identified.
Factors such as whether the camera captures transmitted or reflected light from the product, and whether the lighting should be closer to or farther from the product, are considered to determine the most suitable approach.
(2) Eliminating Blind Spots in the Inspection Area.
Another element in position control is devising a method to ensure that the "imaging captures the entire determination range of the product" without omissions.
For instance, if the product is a flat plate and only one side needs to be inspected, imaging the inspection surface head-on allows for a comprehensive determination without any omissions.
However, for a cubic product with all six sides needing inspection, the following points need consideration:
・Whether it is necessary to take six images directly in front of each side of the cube, or if it is sufficient to take two images from an oblique angle, capturing three sides each.
・Considerations such as the available cycle time for detection, the permissible amount for capital investment, and the presence of transport before and after the inspection should guide decisions on whether to move the product, move the camera, or increase the number of cameras.
"Optimizing the Lighting" and "Eliminating Blind Spots in the Inspection Area." are interdependent.
Often, due to multiple constraints (i.e., limited options), the optimization of lighting is evaluated first, followed by the consideration of control methods to eliminate inspection blind spots.
However, if defect detection through image processing is not feasible in the first place, then deliberating product or camera position control is meaningless.
Therefore, it is common to first verify if defects visible in the images can be detected by image processing before proceeding with discussions on the control of product or camera positioning.
2. Conveyance and Sorting of Products
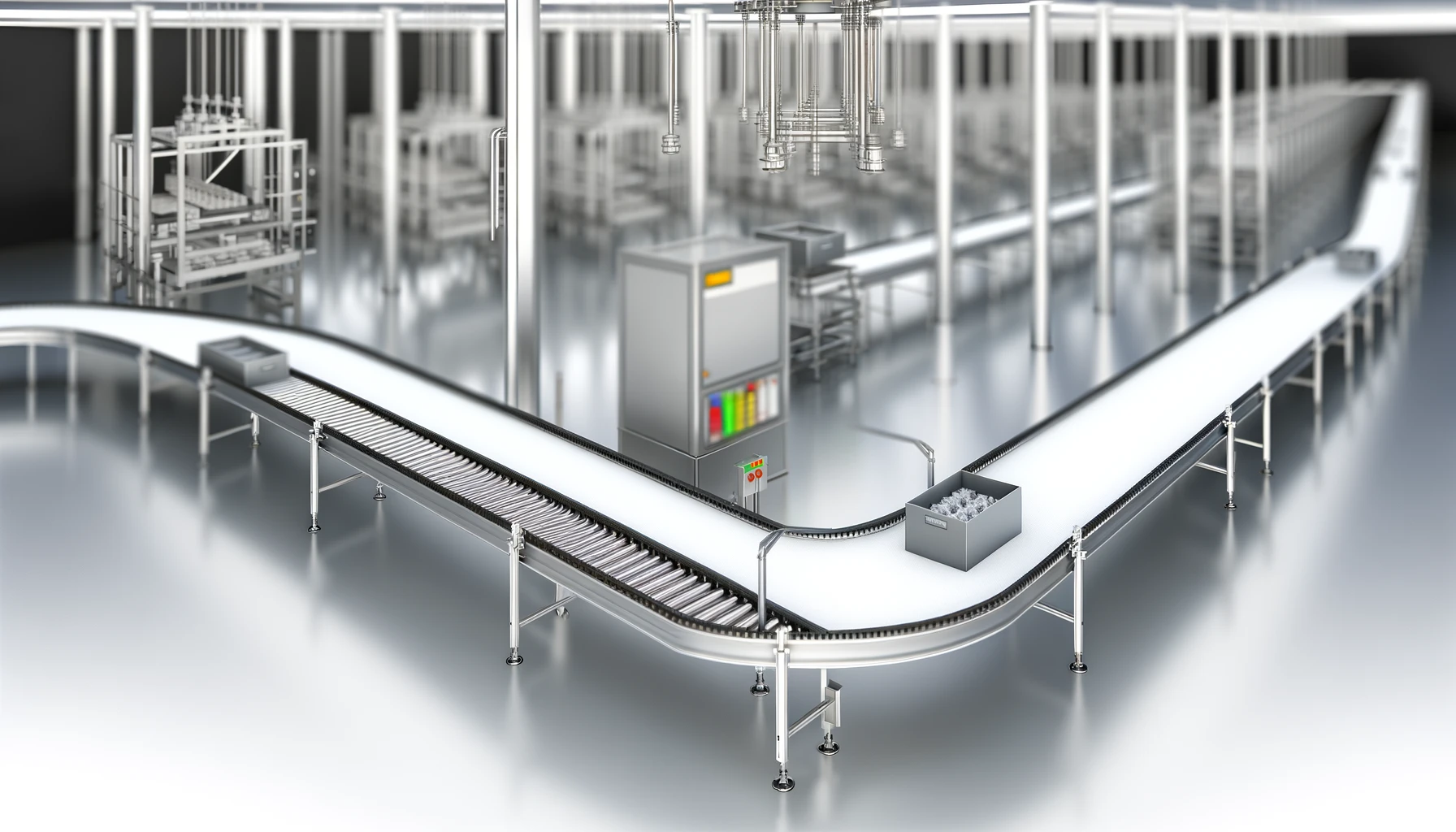
Before conducting visual inspection via image processing, it's crucial to consider how product conveyance and sorting will be carried out before and after the inspection.
While manual handling is an option, the introduction of handling automation is also a consideration.
Factors to consider in this regard include the "Scope of Automation," "Cycle Time," and "Equipment Investment Cost."
Expanding the scope of automation increases equipment investment costs but reduces human involvement.
Additionally, expanding the scope of automation stabilizes cycle times.
However, careful consideration is required as challenges such as a lack of reduction in cycle time or excessive investment may arise.
<Consideration Items for Conveyance and Sorting Methods>
(1) Internal Inspection vs. External Inspection
In the case of off-line inspection, a separate space is designated for inspection apart from the production line, where products brought to this space are evaluated using an image processing system.
Therefore, when considering transport and sorting, it is necessary to plan for the retrieval of products according to their shape and storage method, conveyance to the image processing system, sorting based on the results of the determination, and the discharge of products.
On the other hand, when incorporating an image processing system into an automated line with existing equipment such as conveyors or robots, it is necessary to integrate the image processing system with the control of the existing facilities.
In either case, the purpose of introducing the image processing inspection system, current workflow and cycle time, and the budget for equipment investment need to be taking into account to determine the extent of automation and to design accordingly.
(2) Manual vs. Automated System
As a result of various considerations, using an image processing system for detection does not necessarily require automation of transport and sorting.
For instance, if humans handle the transport and sorting, the image processing system can be tasked solely with the function of pass/fail determination. By having humans verify the results, inspectors can operate in a manner similar to traditional visual inspection.
By limiting automation to only the determination function, it is possible to avoid the "variance in determination" that is a drawback of visual inspection, while keeping capital investment low and implementing an image processing system.
On the other hand, when using automated machinery for transport and sorting, it is expected that in addition to stabilizing the accuracy of image-based determination, reducing the need for human labor and moving towards unmanned operations, and stabilizing the speed of determination can be achieved as benefits.
3. Summary
Product handling technology is a crucial skill in maximizing the capabilities of an image processing system.
Through the combination of image processing techniques and product handling, optimization of the production process is achieved, leading to improvements in both quality and productivity.