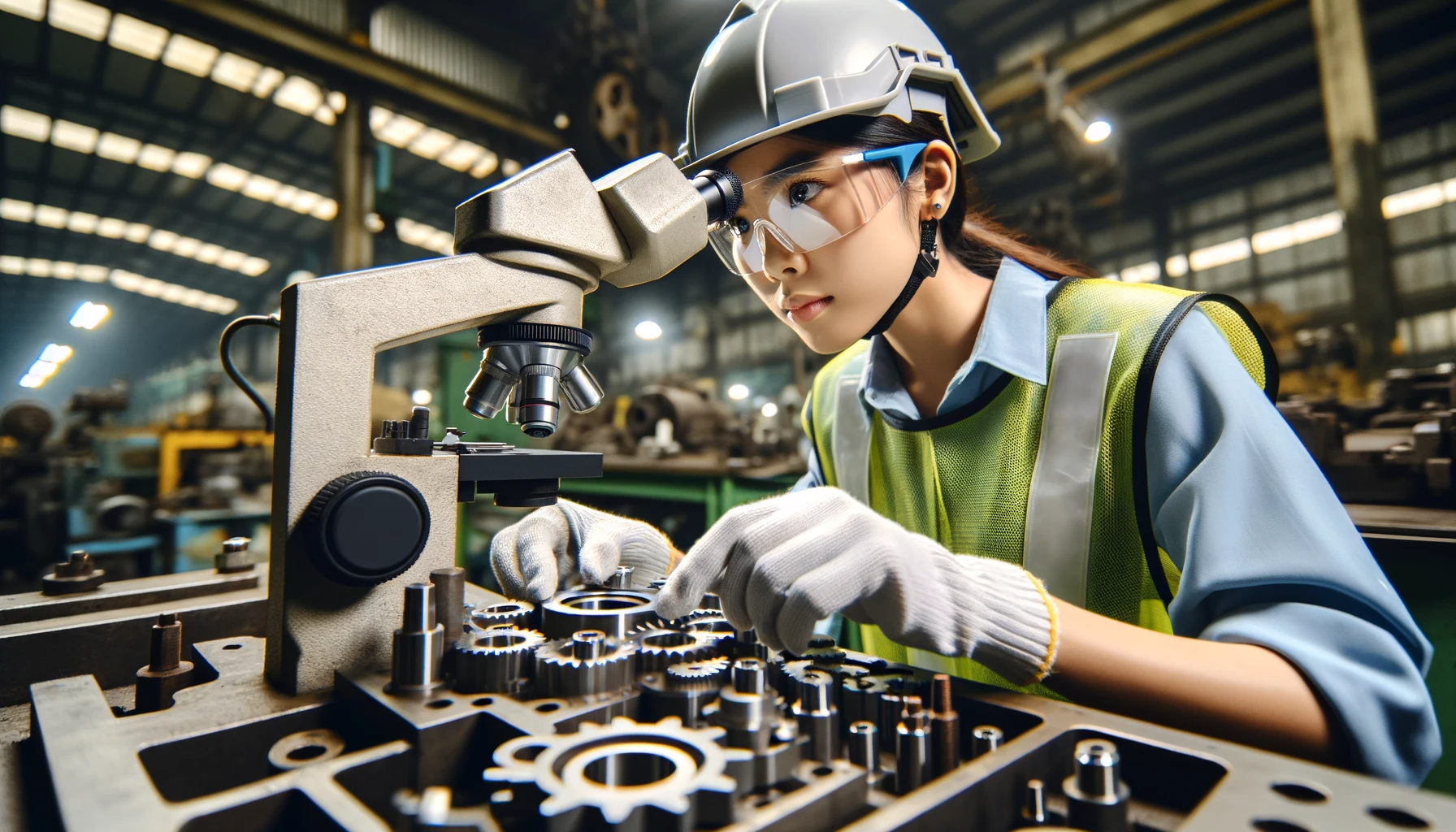
従来のものづくりの現場において、外観検査(製品や部品の表面部分を確認する検査業務)は、長年経験を積んだ熟練者の目で行われておりました。
昨今の日本の製造業は、少子高齢化、若年層の製造業離れに直面しており、これまで通りの検査業務が継続困難な状況に陥っています。
属人的な業務となりがちな目視による外観検査の代替手段の一つとして注目されているのが画像処理技術の活用です。画像技術の活用に先立って、目視外観検査の現状と課題について見ていきます。
1. 目視外観検査の目的
目視外観検査により判別する品質不良は、「機能面の不良」と「意匠面の不良」に大別されます。適切に良否を判別することで、後工程や顧客への不良流出を防ぐことが一番の目的となります。
(1) 機能面の不良
製品の性能や機能に影響を及ぼすおそれのある不良を目視で判別しているケースです。
「目視で判別しているのに、機能面の不良を判別しているの?」と疑問に思われるかもしれませんが、例えば製品に発生しているヒビ割れや欠け等は、製品に機械特性が要求される場合、機能不良の要因として考えられる場合もあります。
(2) 意匠面の不良
製品の性能や機能に直接の影響がないものの、見た目上で最終使用者から不良と見なされる恐れのある不良を判別しているケースです。
最終的な使用用途が一般消費者向けで、且つ消費者の目に付く部分に適用される製品は、特に意匠面の不良に対して厳しく判別される傾向があります。
いずれの場合も、大きさや色の違い、限度見本と比較して良否の判別を行います。
目視による判別は、特別な設備が不要なため、イニシャルコストが発生しないというメリットがある一方で、目視判別は人に大きく依存する工程の一つでもあり、「人ならでは」の課題を抱えていることも事実です。
2. 目視外観検査の対象
(1) 対象物の有無
- 組立て製品の部品組付け忘れの確認(例:ビスの付け忘れ、等)
- 加工忘れの確認(例:穴空け加工忘れ、等)
- 複数種類の製品がパッケージ化された状態での欠落の確認(例:お弁当の惣菜が全て入っているか、等)
(2) 対象物の位置関係
- 組付けられた製品の位置関係の確認(例:組付けた部品が正しい位置にはめ込まれておらず、隙間が空いている、等)
- 本来あるべき場所との整合性の確認(例:組み立て部品において、正しい場所に正しい部品が組付けられていない)
(3) 表面状態や形状
- 製品表面状態の確認(例:製品の色ムラや異物付着、クラックがある、等)
- 製品形状や寸法の確認(例:製品の欠け、寸法異常、等)
3. まとめ
このように、外観検査は後工程や顧客への不良流出を防ぐために必要不可欠なプロセスです。一方で、目視で判別可能な異常は多岐に渡り、対象製品や判別したい内容に応じて検査基準やルールに基づき人間ならではの柔軟性により臨機応変に対応しているのが現状です。
+++ よく見られている記事 +++