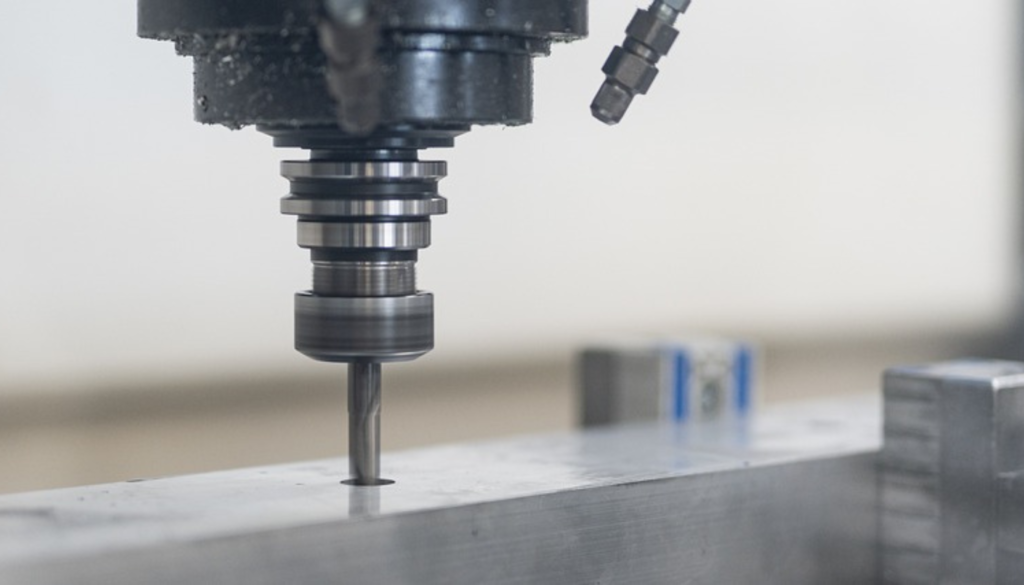
画像処理技術を用いた外観検査は、「対象部品の有無や組付け間違い」、「形状に関する不具合」、「表面特性に関する不具合」、「印刷チェック・数量のカウント」等、目的に応じて様々な検査に使用できます。
ここでは、「対象部品の有無や組付け間違い」に使用する画像処理技術や判別事例について説明します。
また、製品の種類に焦点を当てた「製品別画像処理による判別事例」もあわせて参照ください。
使用する画像処理技術
「対象部品の有無や組付け間違い」を判別する際は、AI、ルールベースのどちらの技術も使用する可能性があります。(AI、ルールベースについては「合否判別に関わる技術」を参照ください。)
一般論として「ルールベースは不良を言葉で定義しやすい検査に向いており、不良の定義ができれば設定は比較的短時間でできる」、「AIは不良の定義が言葉で説明しにくい検査に向いており、設定には時間がかかりがちだが適用できる範囲は広い」という特徴があります。まずはルールベースによる判別が可能か検討をした上で難しい場合はAIによる判別を検討する、というプロセスを踏むことが大切です。
「対象部品の有無や組付け間違い」の判別を行う場合、ルールベースやAIの技術がどのような場面で適しているか参考にして頂けるよう、適しているケースを以下の表に示します。
ルールベースが適しているケース | AIが適しているケース |
---|---|
・有無を確認したい対象が、色で他の対象と明確に切り分けることができる(例:取り付けられている部品の色が他の部分と大きく異なる、等) ・対象部品の位置が常に決められた箇所に取り付けられている(例:画像内で同じ位置にあるビス穴にビスがあるか確認する、等) ・製品形状がシンプルで、照明を均一にあてることができる (例:平板の中の穴開け加工の確認、等) | ・色の情報で対象の有無の確認が難しい(例:部品を取り付ける製品と、部品との色が両方とも黒色で色の差が小さい、等) ・対象部品の位置が変わることもあるが、画像内のどこかにあれば不良とはならない(例:画像の中に決められた個数が確認できれば良品の場合、等) ・製品形状が複雑で、画角内に照明を均一に当てることができない(例:穴開けの有無を確認する際に、製品に凹凸があり、照明を均一に当てることができず、影と穴との色の差を識別できない、等) |
判別事例
プレス部品におけるタップの加工忘れの検出
プレス部品では、部品そのものに発生しているキズやカス上がり、バリなどの外観不良の検査に加えて、プレス後に行う穴開け加工やタップ加工が確実に行われているかを確認する検査もあります。百箇所を越える穴開け、タップ加工が施されている製品もあり、1つの面に対して多くの箇所を人よりも早く、正確に検査ができる画像処理技術は重宝されます。
金属加工製品全般において画像処理判別を行う上では、照明が製品表面に写り込んで発生する白飛び(ハレーション)への注意が必要です。照明の機器選定と照明、ワーク、カメラの位置関係の調整が重要です。
実装基板上の部品付け忘れやハンダ有無の判別
実装基板上の検査は、画像処理による判別で最も歴史ある領域の一つです。実装基板では、数十点に及ぶ基板上への部品の取り付けがあるため、正しい部品が正しい場所に取り付けられているか、ハンダ付けが適切に行われているか、等が判別されます。
基板上の部品の取り付け有無は、平面状に並べられた部品の有無を検査するため、ルールベースによる判別が得意な領域です。一方で、ハンダ付けの有無は基板上のパターンとハンダの色の識別が困難なケースがあるため、AIによる判別が期待される領域です。
使用部品の集積(キッティング)の判別
組立工程でよくある事前準備として、組立に必要な部品を在庫現場から集めてひとまとめに揃える「キッティング(ピッキング)」と呼ばれる準備工程を経る場合があります。この際に、「キッティング」された部品が正しく揃えられているか確認することで、組付け間違いや、組付け忘れを防ぐことが可能となります。
画像処理によって正しく部品がキッティングされているか確認する上では、部品を重なりなく画像内に収めること、画像上で部品の違いを正しく認識できることが重要です。これらの条件は従来の作業内容では実現しにくい点もあるため、作業工程や撮像場所、部品の管理方法など運用面と合わせて検討する必要があります。
まとめ
対象部品の有無や組付け間違いは、製造工程の下流側で特に検査が必要な内容ですが「組立」などの作業をしながら検査を行う「ながら検査」に依存しているケースもあります。二つの作業を同時に行う「ながら検査」は検査の見落としが発生しやすい検査で、「見落としによる品質不良」や「作業者への精神的な負荷が高い」といったマイナス要素を含んでいます。
画像処理による外観検査はこれらのマイナス要素を払拭できる可能性のある技術です。判別したい内容にあわせて、最適なシステムを構築し運用することが品質の確保や持続的な生産性向上には重要です。