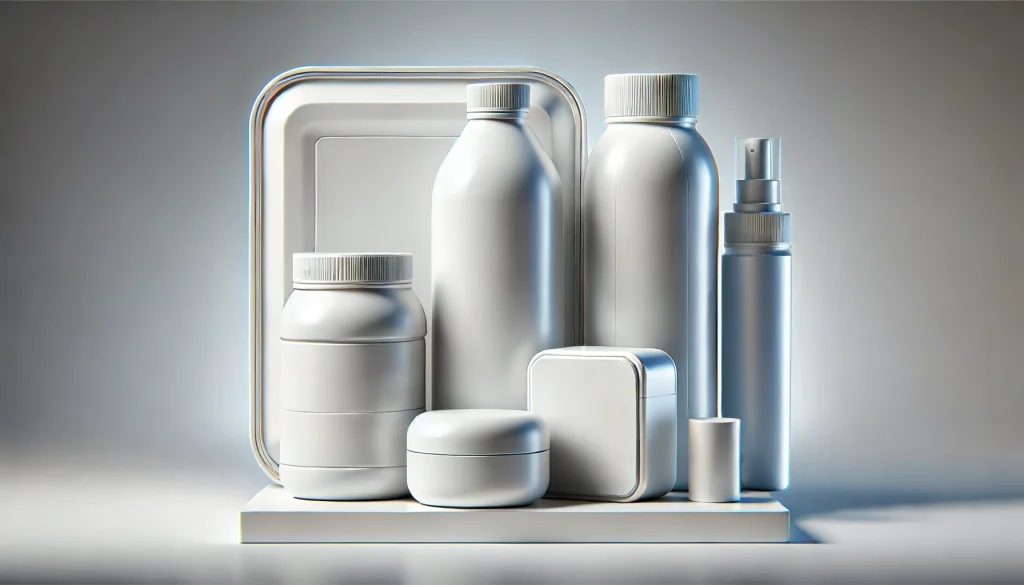
金属製品同様に材質や加工方法の違いにより様々な製品として使用されるのがプラスチック製品です。ここでは、プラスチック製品の成形方法の分類と、成形方法別によくある不良事例、画像処理による判別事例について説明します。
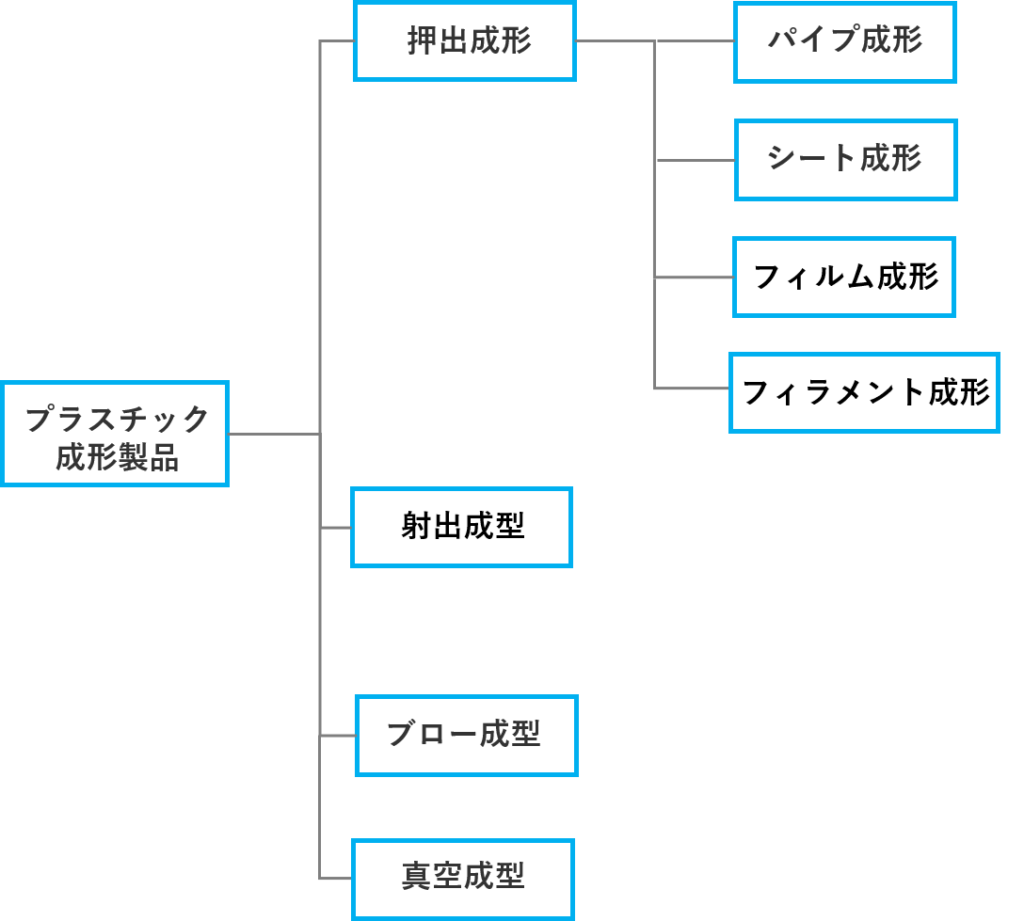
プラスチック製品の分類とよくある不良事例
押出成形
押出成形は、断面形状が変化しないプラスチック製品を連続的に成形する方法です。押出成形では、押出機のシリンダー内にプラスチックの原料を投入し、加熱しながら溶融した上でダイスと呼ばれる押出口から押し出し、冷却することで成形します。ダイスの形状を変えることで、パイプ状、シート状、糸(フィラメント)状に成形することが可能です。押出成形では、スパイダーマーク、フィッシュアイ、オイルマーク、メルトフラクチャー、目ヤニ、ブリードアウト、マイグレーション、コンタミ(異物)といった不良が発生します。
射出成形
射出成形は、押出機のシリンダー内にプラスチックの原料を投入し、加熱しながら溶融するまでは押出成形と同様のプロセスですが、冷却時のプロセスが異なります。射出成形では、溶融したプラスチックを金型内に射出することで成形します。そのため、押出成形に比べて複雑な形状の製品や、3次元形状の成形品を成形することが可能です。
射出成形では、バリ、ショートショット(ショートモールド)、シルバーストリーク、フローマーク、ヒケ、ヤケ、コンタミ(異物)といった不良が発生します。
ブロー成形
ブロー成形は、押出機のシリンダー内にプラスチックの原料を投入し、加熱しながら溶融した原料を金型内へチューブ状に押し出し、内側から圧縮エアーを送り込んで金型に押し当て、冷却することで成形します。ブロー成形では、ヒケ、バリ、コンタミ、偏肉、折れ肉といった不良が発生します。
◆ 射出成形とブロー成形の違いは?
どちらの成形方法も金型の形状によって成形するという点は同じですが、それぞれ以下のメリット、デメリットがあるといわれています。
メリット | デメリット | |
---|---|---|
射出成形 | 複雑で寸法精度が高いな成形品の対応が可能 | 金型の初期投資額がブロー成形対比で高額になりがち |
ブロー成形 | 金型の初期投資額が射出成形対比で安価 射出成形対比で成形時間が短い | 成形できる形状に制約がある(空洞が必要) 寸法精度が射出成形対比で悪い |
プラスチック製品の画像処理による不良判別事例
ここからは、画像処理による判別事例を説明します。
透明プラスチック製品のシルバーストリーク判別
プラスチックを製品に用いる場合、プラスチックの透明性を活かした製品化がなされることもあります。一方で、透明な製品は光を透過するため、撮像する際に透けて見える検査面以外が悪影響し検査精度を落とす要因となるケースがあります。
プラスチックに関わらず、透明体を画像処理により判別する際は透過光を用いることで判別したい不良を画像内で「影」として捉えやすくなるケースが多くあります。このように、画像処理ならではの撮像環境を構築することでより正確な検査が実現可能となる場合もあります。
射出成形品のヒケ検査
プラスチック製品において、画像処理による検査が最も難しい不良の一つが「ヒケ」です。ヒケは、人が目視検査をする際も製品を傾けたりすることで表面への照明の当て方を工夫し、わずかな窪みを視認していますが、この検査環境をカメラ、照明、製品表面の位置関係を調整することで再現し、画像上に写す必要があります。
多くの場合、ヒケは製品表面で照明が全反射したすぐ側で顕著に捉えることができます。そのため、照明と製品とカメラの位置関係が調整しやすいラインスキャンカメラを用いて、照明の全反射光から少し離れた位置をカメラで撮像しながら製品を移動し連続して撮像することで捉えることが可能となります。
真空成形品のシワや偏肉の検出
真空成形で生産される製品の一つに食品トレーがあります。多くの食品トレーでは、極力薄いシートでの強度担保や、内容物を取りやすくする観点から底面に凹凸形状を形成しています。この凹凸形状部分を形成する際に厚みが著しく薄くなってしまう偏肉や、上手く金型にシートが沿わない場合にシワが発生してしまい、食品トレーの密閉性が損なわれてしまう不具合に繋がります。通常、食品トレーは重ねた状態で梱包、出荷されますが、これらの偏肉やシワを検査する際には、全面を確実に検査するため、重ねる前の複数の食品トレーがシート状に繋がった半製品の状態で検査をする必要があるため、製品の搬送速度や撮像のタイミングに加えて、カメラや照明を設置可能な場所が確保できるか、といった点を解決する必要があります。また、食品トレーの壁面を確実に検査するためには、複数方向からカメラでの撮像が必要となるケースもあります。
まとめ
加工性の高さから多種多様な色や形状の製品があり、画像処理による判別が簡単な製品から難しい製品まで多岐にわたるのがプラスチック製品です。発生する不良の特性を理解し、最適な撮像環境の構築や判別のための適切なアルゴリズムの選定が正確な検査を行う上では重要です。