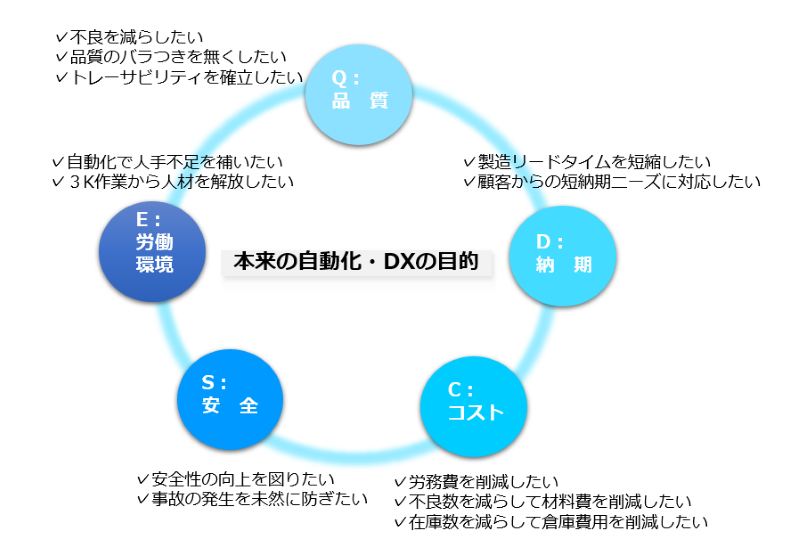
製造業における競争力の強化と効率的な生産体制の構築は、日々進化する技術を取り入れることによって実現されます。その中でも、画像処理技術の活用による製品の判別自動化は、品質向上とコスト削減を実現する重要な手段の一つです。一方で、注意が必要なのは「自動化は手段に過ぎず、目的ではない」ということです。画像処理技術による判別の自動化を検討する際、最初に行うのは、その導入によって達成したい目的の明確化です。目的が不明瞭なまま技術導入を進めると、結果として本来得たい導入効果が得られないケースや部分最適の発生により、導入したものの使わなくなり期待外れの投資になるリスクが高まりますので、以下のステップを考えることが重要です。
ステップ1:目的の明確化
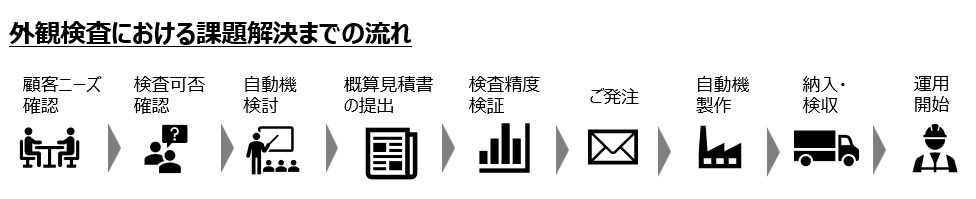
自動化という手段を通じて、何を達成したいのかを明確にした上で“どこまで自動化するのか”を確認します。例えば、人による検査バラツキの抑制により品質の向上を目的とする場合は、製品の投入や搬送、仕分けは人が行った方が、これらを設備で行うよりも設備投資としては少額で収まります。一方で、例えば検査人員の確保が難しいため、無人による判別を行いたい場合は、製品の投入や搬送、仕分けを含めて設備化が必要となります。
ステップ2:対象製品に対する検査可否の確認
正確に画像処理による判別を行う上で、カメラ/照明の機器/製品との位置関係に、どのような制約条件があるか確認します。例えば、対象製品の微細な欠陥を判別するための撮影には、対象製品のどの部分を撮影するのか、どのカメラ、どの照明を使うのか、それらをどのような位置や距離に配置するかといった点が重要です。
ステップ3:前後工程や判別実施時のオペレーションの確認
前後工程のサイクルタイムや品種切り替えの頻度、オペレーターに任せられる操作の範囲、不良と判別した製品の取り扱い等、生産現場に実際にシステムを導入した後のことを想定し、自動機を検討する際の制約条件としてまとめます。その際には、以下の点も考慮します。
既存の生産ラインとの連携:自動化システムが既存の生産設備やプロセスにどのように統合されるか。
データ管理と分析:収集される画像データの管理方法や、不良品検出後のデータ分析の仕組み。
拡張性と将来性:将来的に生産ラインが変更または拡張された場合に、システムが柔軟に対応できるか。
ステップ4:要件定義
ステップ2、ステップ3で確認した制約条件や要望を要件定義として纏め、設計者はこの要件定義に基づいて画像処理判別の構成案を設計します。
ステップ5:設計の実施
要件定義に基づいて画像処理判別システムの設計を行います。設計は、基本設計と詳細設計の2つに分けられます。
基本設計:要件定義で定めた要求事項をシステム的にどのように実現できるのかを明確にし、概略構成案を設計する作業です。多くの場合は基本設計完了後、多大な工数が発生する詳細設計に移行する前に、概算見積書を入手。本見積書と概略構成案により導入検討を行っている会社は投資に見合うか判断します。
詳細設計:基本設計の内容を元に、システムの構造や部品の図面の作成、使用する部品の確定、制御・動作仕様を検討します。
まとめ
画像処理判別システム以外にも該当する話ですが、導入を検討している会社における「当たり前」が、対外的には「当たり前ではない」ケースが多々あります。画像処理に関する制約条件の抽出はもちろんのこと、工程全体を捉まえた際に社内の「暗黙知」が言語化され、制約条件や要件に落とし込まれているかが導入後の「こんなはずではなかった」を避ける上で重要なポイントとなります。