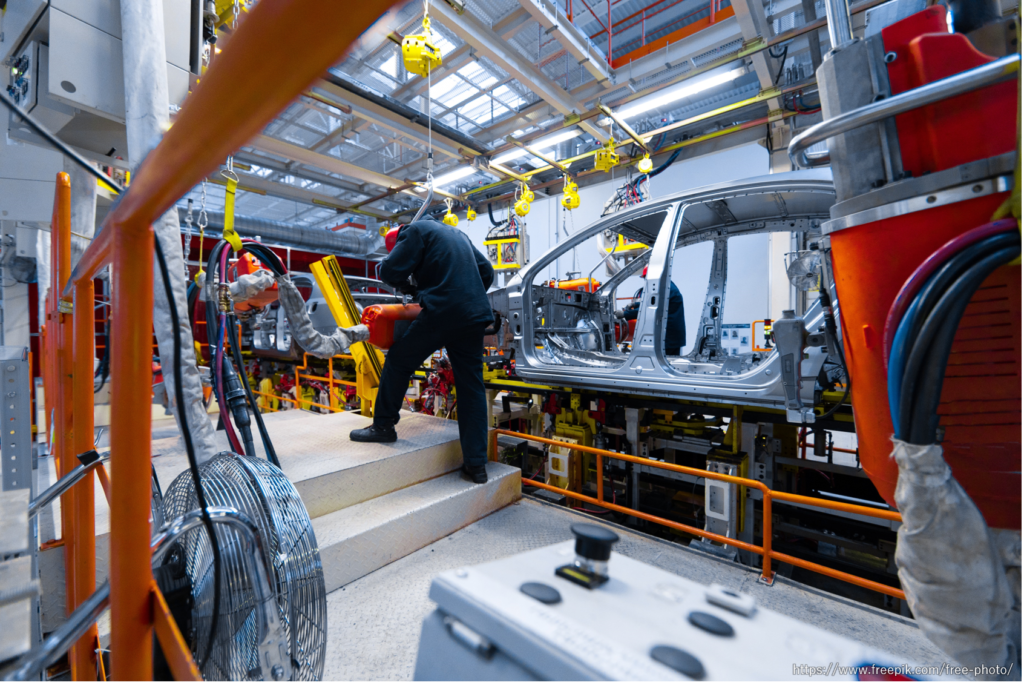
組立製品は、組付ける部品が数mm未満の基板実装を行う電子機器や組立工程において機械加工で調整しながら組付ける精密機器、数百点、数千点に及ぶ部品を組立てる電気機器、自動車をはじめとした輸送機器の他、生産設備向けの産業機器等、様々な製品があります。ここでは、組立製品の分類と、各製品別によくある不良事例、画像処理による判別事例について説明します。
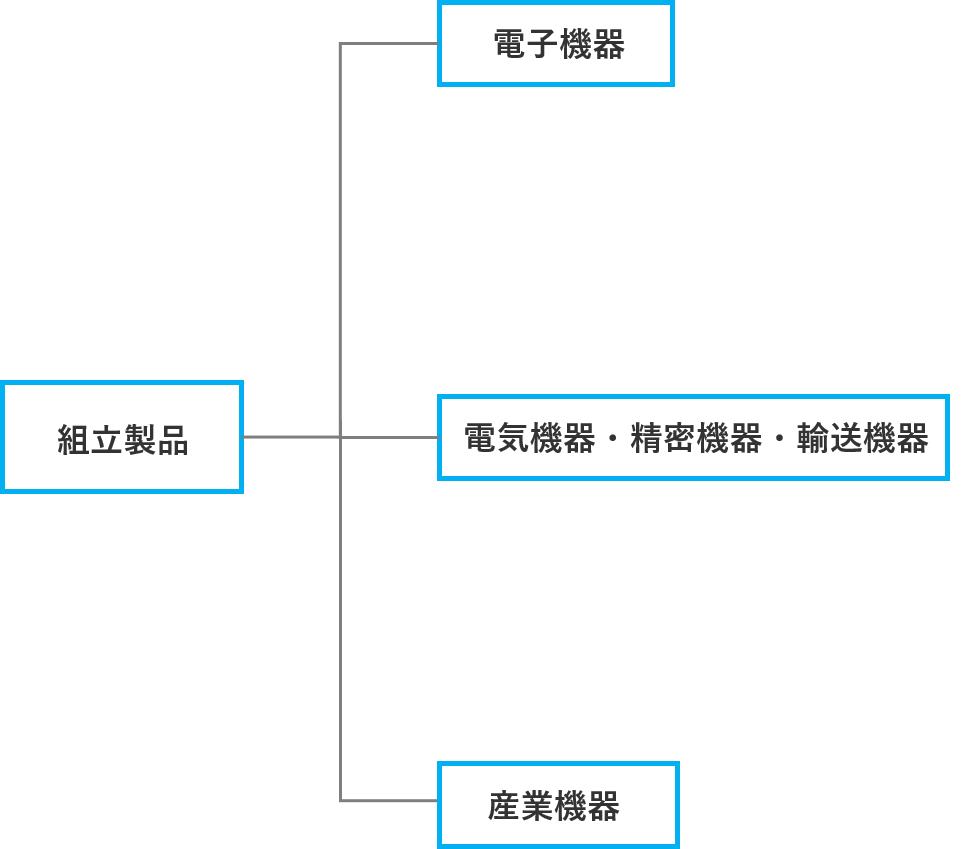
組立製品の分類とよくある不良事例
電子機器
プリント基板上にトランジスタやダイオードICなどの取り付けや、基板上の端子間に配線を行った上でハンダ付けを行うのが電子機器組立です。組立てられた製品の多くは、電気機器や精密機器の部品として用いられます。
電子機器の組み立て時に発生する不良としては、トランジスタやダイオードといった部品の付け忘れや付け間違い、ハンダ不良、ハンダ付け時の横端子とのリークなどがあります。
電気機器・精密機器・輸送機器
生産ライン上に流れる製品に複数の部品を取り付けて完成製品に仕上げるのが電気機器・精密機器・輸送機器における組立です。電気機器・精密機器として代表的な製品としては白物家電やAV機器、OA機器、自動車用電気部品等があります。また、輸送機器には自動車や自動二輪車、鉄道車両などが該当します。
これらの機器の組立で発生する不良としては、部品の組付け忘れ、組付け位置の間違い、別部品の取り付け、嵌め込み不良などがあります。また、実際は部品として生産時点で発生しているキズや汚れなど不良を組立工程で判別しているケースもあります。
産業機器
生産工程で使用される機器などを要求仕様に合わせて部品を組み合わせて組立てを行うのが産業機器組立です。場合によっては一品一様となる場合もあります。また、製品の要求精度によっては旋盤やフライス盤、平面研削盤といった機械加工とヤスリによる手作業を行いながら製品の組立を行う場合もあります。
産業機器組立で発生する不良としては、部品の取り付け忘れや加工時のキズ等があります。
組立製品の画像処理による判別事例
ここからは、画像処理による不良判別事例を説明します。
実装基板上の部品付け忘れ・ハンダ不良の判別
実装基板上の検査は、画像処理による判別で最も歴史ある領域の一つです。実装基板では、数十点に及ぶ基板上への部品の取り付けがあるため、正しい部品が正しい場所に取り付けられているか、ハンダ付けが適切に行われているか、等が判別されます。
部品の取り付け有無は、ルールベースによる判別が得意な領域ですが、ハンダ付けの良し悪しはハンダの有無だけではなくハンダの状態を見ながら「イモハンダ」、「テンプラハンダ」、「ツノ」といった不良を見つける必要があるためAIによる判別が期待される領域です。
使用部品の集積(キッティング)の判別
組立工程でよくある事前準備として、組立に必要な部品を在庫場所から集めてひとまとめに揃える「キッティング(ピッキング)」と呼ばれる準備作業を経る場合があります。この際に、「キッティング」された部品が正しく揃えられているか確認することで、組付け間違いや、組付け忘れを防ぐことが可能となります。
画像処理によって正しく部品がキッティングされているか確認する上では、部品を重なりなく画像内に収めること、画像上で部品の違いを正しく認識できることが重要です。これらは従来の作業内容では実現しにくい点もあるため、作業工程や撮像場所、部品の管理方法など運用面と合わせて検討する必要があります。
まとめ
多くの製品は何らかの形で組み立てられた後に顧客の手に渡るため、製品品質確保の最後の砦として重要な位置付けを組立工程は担っています。従来の目視検査の一部を画像処理による判別に置き換えるだけでも目視検査者の負荷は減らすことが可能となり、検査品質の向上に繋がります。また、部品の有無は比較的簡易な画像処理で判別できる場合もあるため、組立工程において「何を目視検査しているのか」を分解し、一つずつ画像処理判別への置き換えが可能か確認することが大切です。